Collaboration paves the way for seamless design and construction on the new CoBank Center
WORDS: Clinton Waiz
Construction is fertile ground for complications. Beginning with the basic on-time/on-budget obligations despite circumstantial uncertainties like weather, and material and subcontractor availability, general contractors assume a fair amount of risk long before ever breaking ground. Mix in the need to truly understand and achieve the owner’s long-term vision and the process of working with architects, engineers, stakeholders and the various authorities having jurisdiction on a particular jobsite, and myriad potential hurdles grow exponentially. While every contractor’s approach is unique, few would disagree that collaboration is essential.
For Adolfson & Peterson Construction, a national firm with a Colorado presence for more than 30 years, collaboration is more than just a process, it’s a promise.
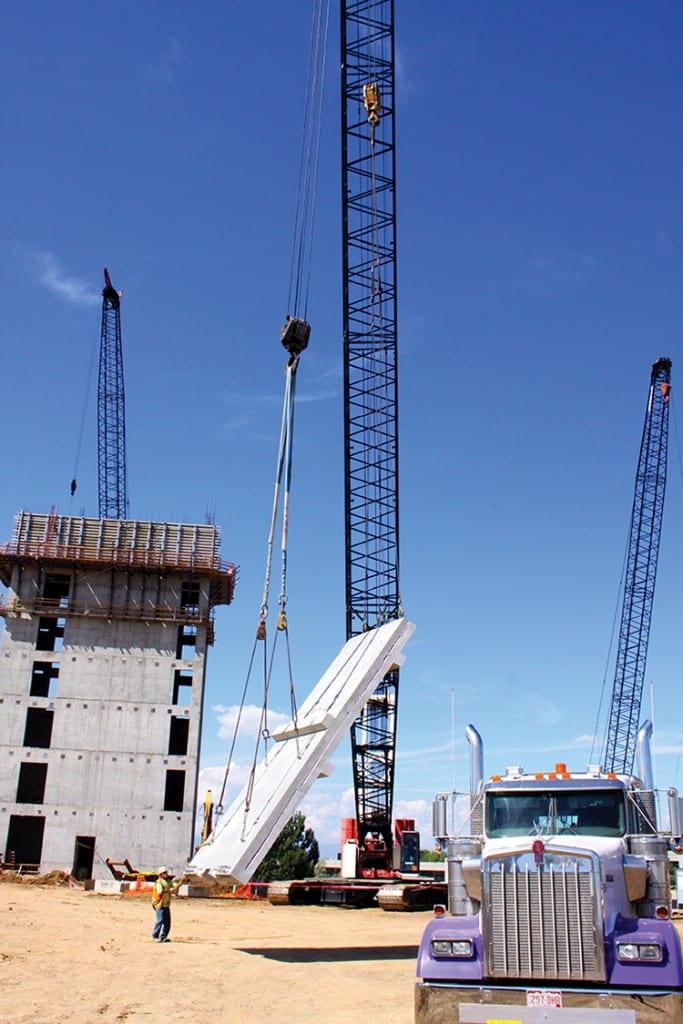
A piece of precast concrete is delivered to the site, ready for placement. The heaviest piece weighed 32 tons. Courtesy Adolfson & Peterson
The latest evidence of the success of A&P’s approach is the CoBank Center located adjacent to Interstate 25 in the Denver Tech Center. This new 11-story, 296,000-square-foot Class A office building will serve as the headquarters for CoBank, a national cooperative bank serving vital industries across rural America from agriculture to water, and communications to power resources. Under the leadership of national developer Shea Properties, A&P was contracted as construction
manager/general contractor through a competitive best value selection process. A key merit of CM/GC is that while the contractor and design team are contracted independently, they are jointly responsible for solving design and construction challenges.
“A&P’s ‘Value Beyond Building’ philosophy is fundamentally about making a personal investment in the long-term success of the project and the surrounding community,” comments Project Manager Ryan Anderson, a construction professional with 17 years of experience. “Maximizing the value of every dollar and every decision made targets a finished product that meets user needs and exceeds owner expectations.”
When A&P was brought on board in January 2014, it joined the ownership team and a dual-architect design team led jointly by Davis Partnership (core/shell) and RNL (tenant finishes). With both architects having independent mechanical, electrical and plumbing design consultants and an interwoven series of core/shell and tenant finish areas overlapping within the building, the importance of collaboration was magnified. Since core/shell design necessarily advances faster than tenant finish drawings, one of A&P’s key responsibilities during preconstruction was to ensure a seamless overlap during construction. For example, the central stair tower is a core/shell component but logically interfaces with the tenant finishes for each floor to accommodate IT cabling, material choices and the precise alignment of internal connections. By taking a leadership role in team communications and incorporating comprehensive 3-D building information modeling, A&P worked to balance all interests and maintain steady design progress.