Just when owners and operators thought they had figured out all they needed to know about refrigerants, the Environmental Protection Agency upped the ante. The new year has ushered in several changes to Section 608 of the Clean Air Act. Section 608, part of Title VI which was an amendment added to the Clean Air Act after the ratification of the 1987 Montreal Protocol, outlines proper management practices for the refrigerants utilized in most of the refrigeration, air-conditioning and heat-pump equipment used in commercial buildings. The intent is to manage and reduce the amount of ozone depleting substances being released into the atmosphere in the United States.
These changes tighten the acceptable leak rate thresholds and increase the consequences for exceeding them. The owner/operator will be required to keep and maintain detailed records to avoid hefty fines.
Types of refrigerant and common appliances. The leak rate changes affect not only known ozone depleting compounds, such as chlorofluorocarbons and hydrochlorofluorocarbons, but also their substitutes like hydrofluorocarbons. Commercial building owners should expect to see these refrigerants used in most air-conditioning applications such as chillers, rooftop-packaged units, split systems and heat pumps. This includes new equipment that has been replaced in an effort to move away from phased-out refrigerants such as R22. In addition, properties that include kitchens with refrigeration equipment, such as walk-in coolers, commercial refrigerators or reach-in coolers, should expect to be affected. Other potential equipment includes cooling for industrial processes or server rooms.
Leak rates. The leak rate must be calculated every time refrigerant is added to a nonexempt appliance that contains greater than or equal to 50 pounds of refrigerant. The EPA clarifies that each independent circuit in a machine with multiple circuits is considered a separate appliance.
When calculating leak rates, the EPA recognizes two methods that the owner and operator can use. The first is the annualizing method, which is more predictive and considers the amount of time since the last refrigerant addition and then projects forward for an annualized rate.

How to calculate the annualizing method, which is more predictive and considers the amount of time since the last refrigerant addition and then projects forward for an annualized rate.
The second is the rolling-average method. This method is more historical and takes into consideration all refrigerant additions over the past 365 days, or since the last successful follow-up verification test showing all identified leaks were repaired.

How to calculate the rolling-average method. This method is more historical and takes into consideration all refrigerant additions over the past 365 days, or since the last successful follow-up verification test showing all identified leaks were repaired.
It is important to note that whatever method the owner or operator chooses, the same method must be used for all appliances subject to the leak repair requirements located at an operating facility.
The leak rate thresholds for all nonexempt refrigerants are:
- Industrial process refrigeration – 30 percent lowered from 35 percent.
- Commercial refrigeration – 20 percent lowered from 35 percent.
- Comfort cooling – 10 percent lowered from 15 percent.
If you have a leak and are not in compliance. A certified technician must perform a leak inspection to identify the necessary repairs. Once a leak has been verified, the owner/operator has 30 days to repair the leak, mothball the system or create a retrofit/retirement plan. The EPA is serious. Failure to comply can result in fines of up to $37,500 per day!
Repair. Any repair must bring the appliance below the acceptable leak rate. A certified technician also must conduct two verification tests. This includes an initial verification test (performed before refrigerant is added back into the repaired appliance) and a follow-up verification test (performed after the repaired appliance returns to normal operating characteristics and conditions). There is no minimum waiting period so the tests can be performed the same day. If the initial or follow-up verification tests indicate that repairs were not successful, additional repairs and verification tests may be conducted within the 30-day window.
Retrofit/retirement. Owners and operators must create a retrofit or retirement plan within 30 days of an appliance leaking above the applicable leak rate if:
- The owner/operator intends to retrofit or retire rather than repair the leak.
- The owner/operator fails to identify and repair the leak.
- The appliance continues to leak above the applicable leak rate after required repairs and verification tests.
It is important to note that owners and operators must self-report chronically leaking appliances defined as having lost greater than or equal to 125 percent of its charge in one calendar year. This report must describe efforts to identify and repair leaks and must be submitted no later than March 1 of the following year.
After a leak has been successfully repaired. Congratulations on a successful repair! But not so fast, the EPA wants to see more. The unit will be subject to a variety inspections, outlined in the table, performed by certified technicians.
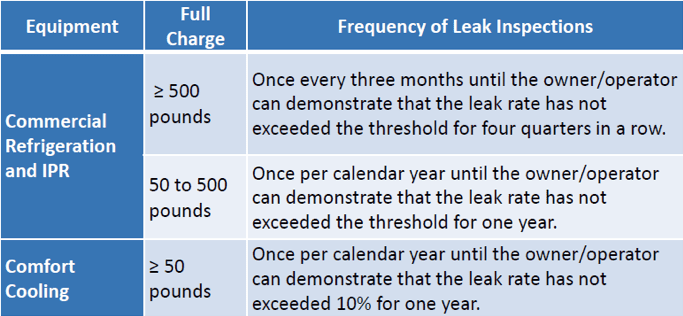
After a successful repair, the unit will be subject to the following inspections performed by certified technicians.
Record keeping. Owners and operators must maintain hard or electronic copies of the following:
- Records documenting the full charge of appliances;
- Records showing when service or maintenance is performed, when refrigerant is added to an appliance (or removed, in the case of disposal), when a leak inspection is performed, and when a verification test is conducted; and
- Records of annual calibration and the date/location of any identified leaks (if using an automatic leak detection system).
In practice, a reputable contractor will perform the calculations and maintain records independent of the owner or operator; however, it is the responsibility of the owner/operator to maintain the documentation, perform the leak rate calculations, and ensure that the equipment stays compliant. After all, they are the ones paying the bill if the EPA comes knocking.
For full details, visit the EPA’s website for refrigerant management regulations.