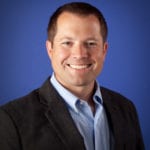
Ted Laszlo
Vice president, Vertix Builders Inc.
Modern medical equipment is advancing rapidly, providing patients with state-of-the-art care and procedures that enhance safety. As an outcome, hospitals are retrofitting existing space in order to integrate modern equipment and technology into their buildings. In some cases, the upgraded spaces are in facilities that are 40 and 50 years old. Needless to say, this comes with many challenges, some of which are difficult to foresee.
From the size of the new equipment, to reconfigured floor plans and existing building constraints, hospitals face critical challenges and risks if they aren’t working with a qualified and knowledgeable team of designers and contractors. When the right team isn’t in place, the ability for a hospital to provide critical medical services in a timely manner is jeopardized, and patients’ care can suffer from a hospital’s inability to perform.
To ensure that the integration of new medical technology and equipment is being appropriately planned for, and the design and construction team is qualified to do the work, there are several important factors to consider.
Existing constraints. Many times, new medical equipment requires larger or reconfigured rooms in which to operate, due to changing procedure workflow, equipment layout and clearances, as well as corresponding support corresponding spaces. This means that existing procedure rooms may need to be expanded in order to accommodate the equipment and technology.
Because so many hospitals were built 50 years ago or more, it’s imperative that the team gather all of the existing condition data available. This would include original plans and as-builts to identify possible challenges for the expansion (including utilities, existing structure, chases, etc., that lie within the walls and above the ceiling). Typically, these documents will tell only half the story as so many changes and additions occur over time in medical facilities. So, to the greatest extent possible, the team should endeavor to survey and document existing conditions where possible.
Weight limitations. Not only does the size of new equipment need to be taken into consideration, but so does its weight. Operating and lighting booms can add significant loads to the existing structure and in new locations where support may not be available. As new mechanical and electrical equipment are added to support the new spaces, new air handling units, for example, additional structure support may need to be added.
The key to success here is not the new structure, but how the new connections impact existing spaces and create new constraints. As a result, the team will need to be prepared to find creative ways to reroute utilities, penetrate fire barriers, etc., to accommodate the new structure.
Finalize equipment decisions. Due to the intricacies of modern medical equipment and their robotics, very little is standard among different manufacturers. Therefore, it’s imperative that the team make its final decisions on the equipment and how the workflow affects its existing facilities to ensure that the solution is designed and built once. Often, changes in vendors or an updated workflow can result in rework to the recently built spaces, leading to significant delays to redesign and rebuild to suit the new equipment.
Create mock-ups. New technology creates new procedure, and in many cases procedures that are different to what the staff are accustomed to. With this in mind, the team should create mock-up rooms for training the medical team and verifying clearance and compliance. The design team, construction team and equipment vendor can work together to create inexpensive but dimensionally accurate spaces where this can occur.
Proven experience. Be sure that your general contractor’s team has proven experience implementing the vision that the facility has worked so hard to create. Not only can you review a team’s past projects and references, but also you can check their training and accreditation from agencies such as the American Society for Healthcare Engineering as Certified Healthcare Constructors or similar designations from a reputable organization as a way to qualify them for sensitive projects. This qualification demonstrates not only a knowledge of best practices working in health care environments, but also a high level of experience executing those practices.
The integration of modern medical equipment demands a unique level of service and attention to detail that isn’t found on other jobsites. With a population that includes patients, family members and caregivers, a hospital should seek out a construction team that is ultimately mindful of the care they’re providing while performing its jobs.