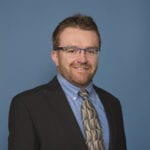
Paul Ruffini
Senior preconstruction manager, RK Mechanical
The health care industry is transforming as new business models emerge to meet the demands of today’s consumers. As life expectancy increases, people are living longer and are seeking conveniently located health care facilities that offer more personal amenities and specialization in clinical areas. Thankfully, prefabrication has allowed health care facilities of all types and sizes to be built faster, more safely and more efficiently.
Prefabrication, also called off-site construction, includes prefabricated construction materials, modularization and/or pre-assembly of manufactured materials. Prefabrication has been around for a long time, but in recent years, new technologies have led to rapid advancement. Off-site construction is an ideal method for delivering projects more quickly and affordably than ever. Plus, prefabrication reduces manpower requirements – a big benefit during our current labor shortage.
But even though prefabrication is a growing trend, building owners and construction industry firms have been slow to adopt this manufacturing-style approach. According to FMI research, FMI: A New Era for Modular Design and Construction, only around 38 percent of owner organizations have a high acceptance level of offsite construction, and close to 50 percent still choose a traditional construction approach.
FMI’s opinion is that the AEC industry “must prioritize technology strategies to innovate corporate cultures and antiquated mindsets to buck the status quo and embrace disruption as an opportunity to win in the future in order to remain relevant.”
By embracing new technologies like advanced off-site construction methods, our industry will be able to keep pace with the increasingly demanding construction needs of the health care industry.
According to Modern Healthcare’s annual Construction & Design Survey, participants predicted that health care industry growth would be the strongest in outpatient and retail clinics because they cater to on-demand consumers who want quick and easy health care options. Microhospitals also are being built more frequently to serve patients who are far away from major hospitals.
The trend toward smaller health care facilities aligns nicely with the latest prefabrication innovations. Many contractors realize that prefabrication can shave weeks or months off of the standard ground-up construction schedule while also offering cost savings, or, at least, more precise cost control due to the lower risk of errors. Shortening the project schedule is key, because the sooner work is complete, the sooner the facility can expand the care it provides.
For example, a hospital patient room usually includes a bathroom, head wall, foot wall and a sink wall. Today, these components can be manufactured off site and assembled quickly on site for greater project speed and efficiency. When materials are built off site, the weather is no longer a cause for delays, and the quality is more consistent.
Another benefit of prefabrication is the ability to achieve consistency – in both quality and design – across several facilities. If your goal is to open 20 facilities that look and feel the same, prefabrication should be considered for as much of the work as possible.
Then there’s safety: Prefabrication creates safer working environments for construction workers, facility personnel and patients (if the building is operational during renovation). Prefabricating construction materials off site can reduce the onsite work by 70 percent or more, so the safety risks associated with construction are greatly reduced. For example, when materials are built off site in a warehouse, then fewer ladders, scaffolding or platforms are needed at the health care facility project site, which minimizes a source of slip and fall hazards.
If a health care facility must remain operational during renovation, then prefabrication is even more essential. This is because construction crews can perform work more quickly and do it with less disturbance to facility employees and patients.
Our mechanical contractors specialize in constructing and installing health care mechanical systems, including plumbing, HVAC and med gas systems. The mechanical systems in a medical facility contribute to sterilization, infection control, imaging equipment, patient hygiene and environmental comfort. Like many other components of a project, the mechanical systems can – and often are – prefabricated. In fact, we BIM and prefabricate much of our plumbing and HVAC systems – and even entire mechanical rooms and central utility plants – for more seamless installation.
Along with a strong knowledge of prefabrication techniques, a good specialty contractor knows that health care construction requires training and experience in the complex requirements of medical facilities. A mechanical contractor with health care experience will take the time to understand the safety and security requirements of each facility before beginning work. The mechanical contractor should serve as an adviser and meet with the design team and project owners regularly. Additionally, a partner should maintain health care related contractor certifications and invest in health care-specific safety training for all team members.
Mechanical contractors, like other trades, are leveraging off-site construction and prefabrication with great success. Prefabrication has proved to increase efficiency through less wasted material and an accelerated schedule. Repetitive processes lead to consistency and fewer mistakes, resulting in better and more consistent quality.
So if you’re a decision maker in hospital or medical facility construction, it’s a good idea to ask project bidders to present their prefabrication capabilities and experience. By accepting the prefabrication trend now instead of later, you could reap many benefits, and complete more projects that meet, or even exceed, your expectations.